When piloting FO membrane elements, high packing density, light-weight, ease-of-use, and flexibility are key advantages
I work as Head of Technology Development at Aquaporin A/S and have been working with forward osmosis technologies for over 10 years. Lately, I have been focusing on FO application testing – more specifically investigating and developing ways to exploit the benefits of forward osmosis for various applications.
The following article builds upon my previous contribution: “New forward osmosis hollow fiber element bridges the gap between lab-scale testing and industrial applications”.
In my opinion, since FO is still not a standard industrial process, a relatively cheap and easy membrane arrangement is needed to be used in pilot and proof of principle studies. The figure below shows an example of what such a membrane arrangement could look like in practice:
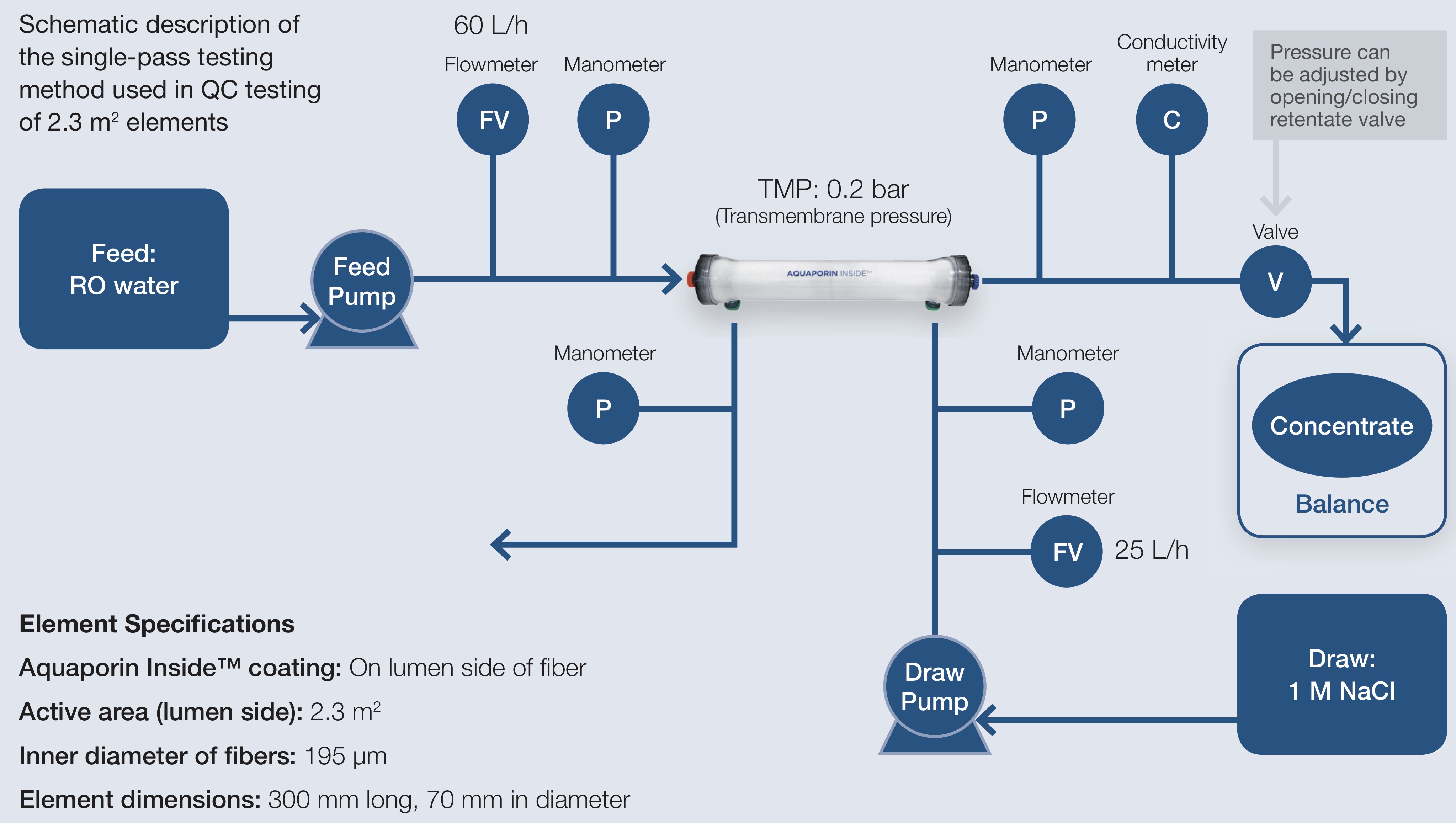
Forward osmosis elements can be connected and integrated in the setup above by standard hose connections. Furthermore, compact elements can be easily connected in a variety of arrangements and thus can prove as a great tool for piloting studies. You could take one as a proof of principle and then add others to push the process to the limits. The added benefit of using compact elements with high packing density is that they are lightweight and easy to handle.
FO application example: treating effluent from dairy plants to meet nitrogen discharge criteria
One of the first pilot systems using a compact hollow fiber forward osmosis element has been installed and tested with a project supported by the IBISS platform (Industrial BIomimetic Sensing and Separation). Here, effluent from a dairy plant needs to be treated and the main goals are to lower the costs of dewatering the whey and increase the purity of final permeate compared to conventional RO. This is one example where increased environmental awareness lead to stricter discharge criteria (in that case of nitrogen) which then challenges the current water treatment installations. Within the IBISS test case, preliminary tests were followed up by a pilot scale test at the site of the collaboration partner. Here, 1m3 of wastewater effluent from different steps of the production process were treated per day. The clean water that is taken out of the waste stream was recovered using traditional RO technology which also re-concentrated the draw to be used in the FO step again. 7 FO elements in total were used with an overall area of 16 m2 in a small-scale pilot system (see the figure below). The system was operated with 50% water recovery, a 0.8M NaCl draw solution and single pass operation mode.
Other FO application examples
FO is a versatile tool for de-watering feed streams that contain valuable products that should not or cannot be exposed to pressure or heat such as concentration of valuable and/or sensitive compounds from the food and beverage industry (e.g. coffee, natural flavors, natural colours, whey, …).
Especially in those applications, the advantages of the hollow fiber module having a small dead volume that can be easier recovered than in spiral wounds and easy cleanability with no no-flow areas offer another step forward in promoting forward osmosis as a viable tool in the filtration industry.
The newest addition to the growing number of industrial FO pilot cases is a hybrid FO system coupled with RO and evaporators to treat wastewater from the semiconductor industry.
What does the future hold for FO?
To sum it all up, FO – in my opinion – is a powerful and versatile tool in the field of water treatment and the addition of new and compact commercially available FO elements now offers a new tool in the toolbox needed to convince the industry that FO can help to solve some of their challenges and that it is worth to try.
Especially, FO membrane elements with low reverse solute flux make a compelling argument for all those that were worried that their feed would be further contaminated or the loss of compounds in draw would be uneconomically.
For more information on FO technologies in general and FO piloting in particular
If the above made you curious, please don’t hesitate to contact me at jvo@aquaporin.dk for more information.