Forward osmosis is one of many new water technologies addressing the growing need for sustainable water resources
The ever-increasing demand for high quality water treatment coupled with increasing water quantity demands has in recent years led to an accelerated development of water treatment and the exploitation of new water sources. The demand for technological development in this area is tremendous and the possibilities numerous. In my eyes, forward osmosis (FO) is one of the key processes in this development. I work as Head of Technology Development at Aquaporin A/S and have been working with biomimetic membranes and their application specifically in FO for over 10 years. At Aquaporin A/S, I am responsible for the integration of the Aquaporin Inside™ technology onto hollow fibers and the Aquaporin Application Lab. Here, ways to exploit the benefits of forward osmosis for various applications are continuously being investigated and developed in collaboration between experienced in-house researchers, universities and companies worldwide.
But forward osmosis technologies need to “grow up” before they can be widely commercialized
There are numerous applications where FO could be used but in my eyes FO should firstly focus on the up-concentration of valuable compounds and the treatment of problematic wastewaters where difficult to remove compounds are present. These very specialized niches offer the opportunity to introduce a new and in the beginning slightly more expensive technology as a solution.
In that regard, it is my opinion that forward osmosis pilot systems must be established to investigate economic feasibility and to show off systems to potential end-users – in simple words, growing up, meaning leaving behind the laboratory stage and entering industrial applications.
In this context, Aquaporin A/S recently launched a new forward osmosis hollow fiber element designed to bring forward osmosis technologies out of the lab an into industrial piloting. I’ll be happy to send more information on this. Just drop me a line at jvo@aquaporin.dk
The main advantage of forward osmosis technologies
To start with, let me just briefly introduce forward osmosis in more detail. Osmosis, in general, is a natural process in which concentration differences between two aqueous solutions that are separated by a semi-permeable membrane cause water transport from the side with a low solute concentration to the side with a high solute concentration. This can be explained by the second law of thermodynamics which states that over time a difference in pressure, temperature or concentration in an isolated physical system will equilibrate. This pursuit of maximum entropy leads to irreversible changes in the system. Usually the two differently concentrated aqueous solutions would mix and solute would diffuse equally in the system. By introducing a semi-permeable membrane that does not allow solute transport, the only way for the system to equilibrate is by water transport from the side with higher solute concentration to the side with lower solute concentration. This natural occurring driving force is exploited by FO and illustrated below.
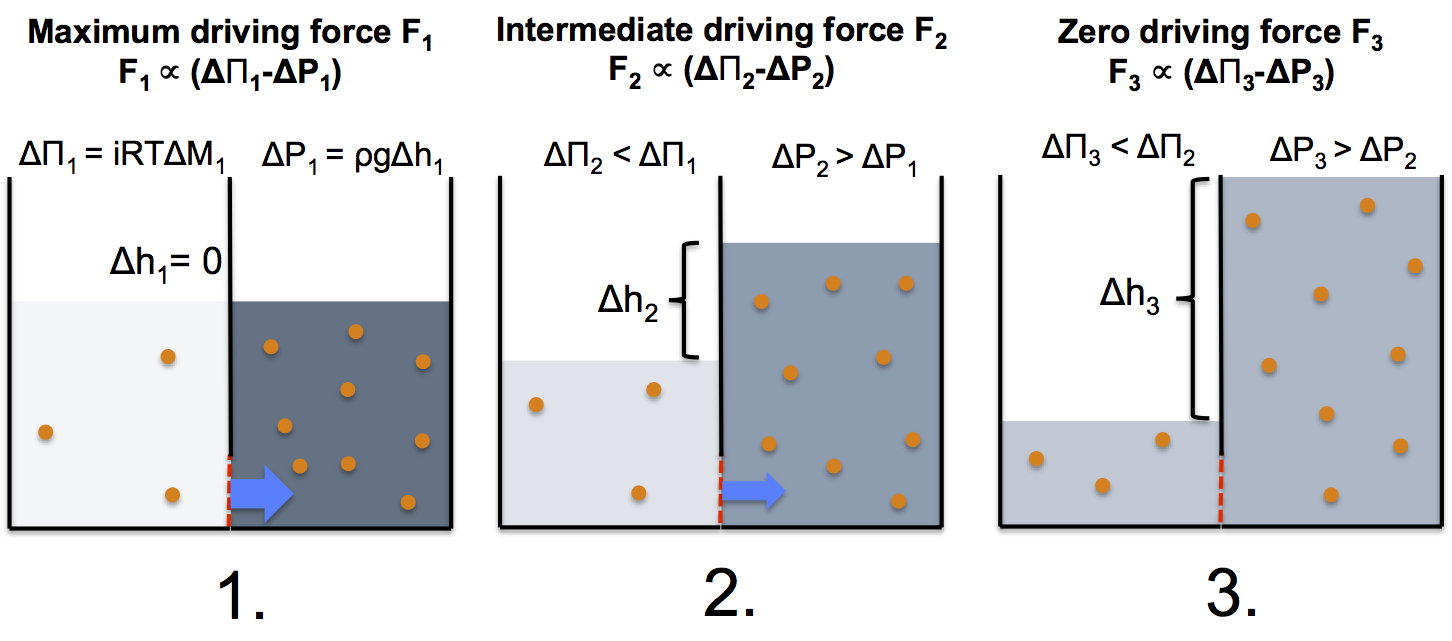
Here lies also the main advantage for forward osmosis because liquids can be treated without using heat or hydraulic pressure which is especially beneficial in applications in the food and beverage area. Also, no high-pressure pumps or pressure resistant materials are needed and CAPEX costs could potentially be far below traditional treatment process. However, for all those benefits there are still two main challenges that remain with FO – draw solution and membranes. Both challenges are investigated by researchers and companies worldwide with great advancements in both fields. In this article, I will put the focus on membranes because to make FO into a commercial success highly selective and efficient membranes are needed. So far, FO as a process technology has not been widely commercialized yet and thus only a handful of companies provide specially designed FO membranes. However, high performance membranes are needed to convince the industry of the viability of FO.
FO membrane performance can be improved through performance enhancing components
Research into improved membranes for FO is ongoing and especially the addition of performance enhancing components into selective layers of membranes has been discussed in industry and literature for years. Scientists have added zeolite particles, carbon nanotubes and even biological components like aquaporin proteins to membranes to increase their performance with regards to water flux and rejection [1-5]. The incorporation of aquaporin proteins to mimic nature’s way of filtering water has received much attention and has been attempted both by universities and researchers in the industry [6-8]. Aquaporin A/S has, as the first company, commercialized the potential of this water channel and is now entering full scale production.
Aquaporin’s technology relies on the incorporation of aquaporin containing vesicles into a thin film composite layer. The proteins are incorporated into a cell-membrane mimicking entity, called a vesicle, where it is ensured that they are correctly folded and active. The vesicles are then embedded into a polyamide layer on top of a support membrane using interfacial polymerization. The process is also described in [9].
Aquaporin’s forward osmosis hollow fiber element
The first commercially available FO product incorporating aquaporin proteins is a 2.3 m2 hollow fiber elements. Especially in FO processes, the high packing density and easy flow patterns of hollow fiber elements are immensely beneficial. The membrane does not experience any mechanical stress and thus can be designed differently from a standard RO membrane. As can be seen in the figure below, the test setup needed for an FO process is relatively simple, just using gearing pumps and hoses and sensors.
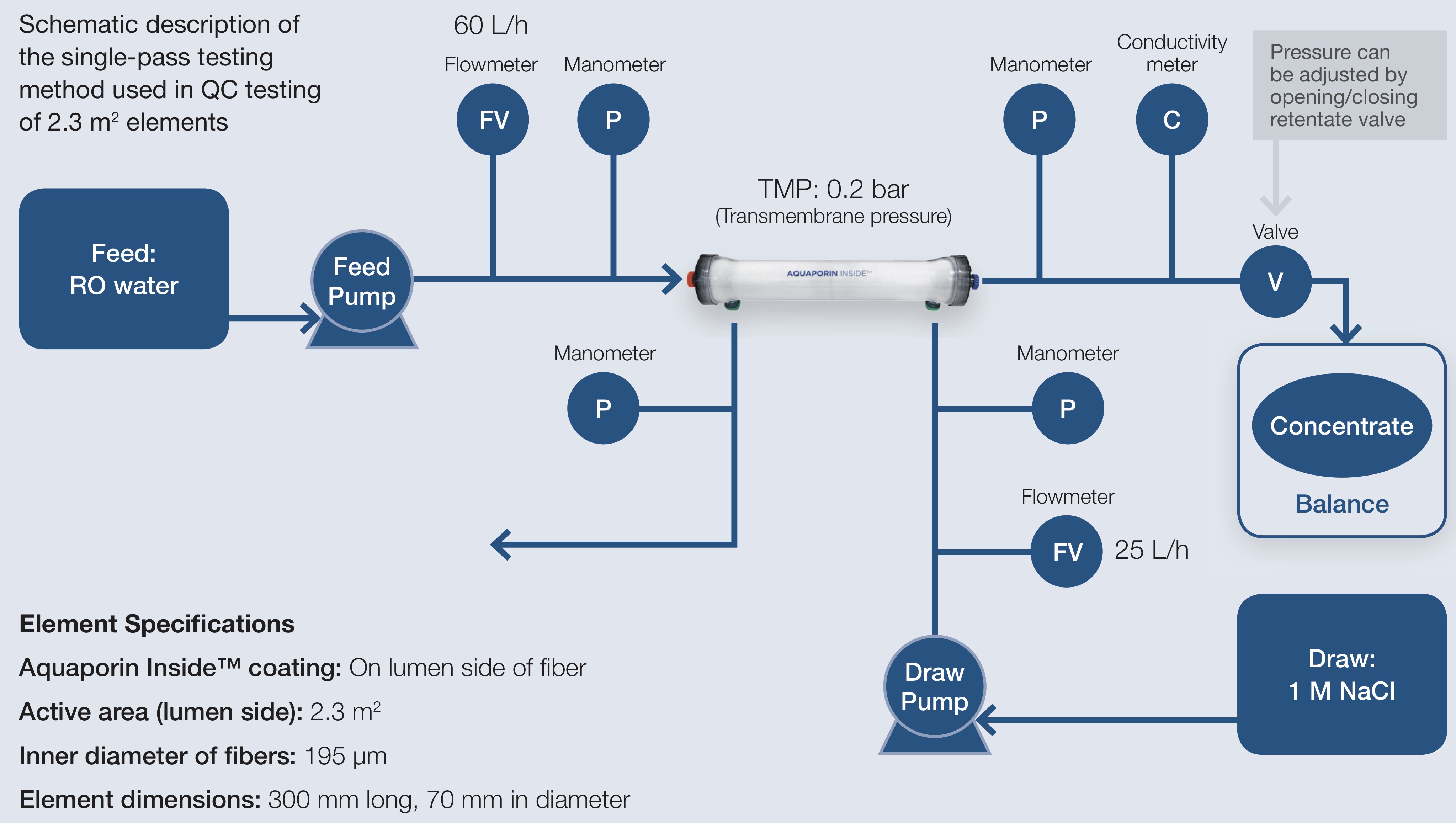
For more information on FO technologies in general and FO piloting in particular
If the above made you curious, please don’t’ hesitate to contact me at jvo@aquaporin.dk for more information.
Look out for my next article contribution, which will zoom-in on specific examples of industrial FO applications.
References
- -H. Jeong, E.M.V. Hoek, Y. Yan, A. Subramani, X. Huang, G. Hurwitz, A.K. Ghosh, A. Jawor, Interfacial polymerization of thin film nanocomposites: a new concept for reverse osmosis membranes, J. Membr. Sci. 294 (2007) 1–7.
- L. Jadav, P.S. Singh, Synthesis of novel silica-polyamide nanocomposite mem- brane with enhanced properties, J. Membr. Sci. 328 (2009) 257–267.
- Yin, E.-S. Kim, J. Yang, B. Deng, Fabrication of a novel thin-film nanocomposite (TFN) membrane containing MCM-41 silica nanoparticles (NPs) for water purification, J. Membr. Sci. 423–424 (2012) 238–246.
- Kulprathipanja, R. W. Neuzil, N. N. Li, Separation of fluids by means of mixed matrix membranes, US 4,740,219 (1988).
- Peyki, A. Rahimpour, M. Jahanshahi, Preparation and characterization of thin film composite reverse osmosis membranes incorporated with hydrophilic SiO2nanoparticles, Desalination 368 (2015) 152–158.
- Kumar, et al., Highly permeable polymeric membranes based on the incorporation of the functional water channel protein Aquaporin Z, Proc. Natl. Acad. Sci. USA 104 (2007) 20719–20724.
- H. Nielsen, Biomimetic membranes for sensor and separation applications, Anal. Bioanal. Chem. 395 (2009) 697–718.
- Y. Tang, et al., Desalination by biomimetic aquaporin membranes: review of status and prospects, Desalination 308 (2013) 34–40.
- Zhao, et al., Synthesis of robust and high-performance aquaporin-based biomimetic membranes by interfacial polymerization- membrane preparation and RO performance characterization, J. Membr. Sci. 423–424 (2012) 422–428.